
Wherever possible, workers should not fabricate silica containing products at the installation site. You can also use barriers around automated tasks to shield workers from silica dust. Providing physical barriers and exclusion zones between different workers and workstations to prevent dust or water mist from moving into other work areas or towards other workersĭistancing a work process from other workers.įor example consider where other workers are working when powered hand tools are usedĭesignating a room or area for other tasks such as changing or eating, away from the work area. Isolating high dust generation work processes within an enclosed room with restricted access Physical barriers that remove the worker from contact with silica dust are the most effective form of isolation controls. Isolation is an effective way of protecting your workers from exposure to silica dust. Isolation is where you place barriers or distance between a hazard and your workers. Isolate workers and others from silica dust Use a liquid or paste form of a silica product. Use a silica containing product that does not need to be cut, ground or polished, and Use products that do not contain silica or have less silica in them Substitution can be an effective way of managing the risk of exposure to silica dust. Again, substitution might not be practicable where silica is naturally occurring or if it means you can’t make the end product or deliver a service. Substitution is where you replace a product or chemical with something that is less hazardous and therefore has a lower risk.Įffective substitution of silica and silica containing products will depend on your workplace and the work tasks your workers carry out. This will effectively remove the risk of workers being exposed to silica dust when working with these products. If it is reasonably practicable, eliminate the silica containing products from your workplace. Treating the dust on its transmission path using dust suppression techniquesįor example water sprays, chemical additives, local exhaust ventilation (LEV), vacuum. Treating the dust at the point of generation, as this is more effective than capturing airborne dust, and For example:Īdopting production processes that generate less dustįor example any wet method is likely to generate less dust than a dry one You can eliminate silica dust at the source by eliminating the processes that generate dust. Elimination may not be possible if silica dust is naturally occurring at your workplace or you can’t make the end product or deliver a service without generating it.
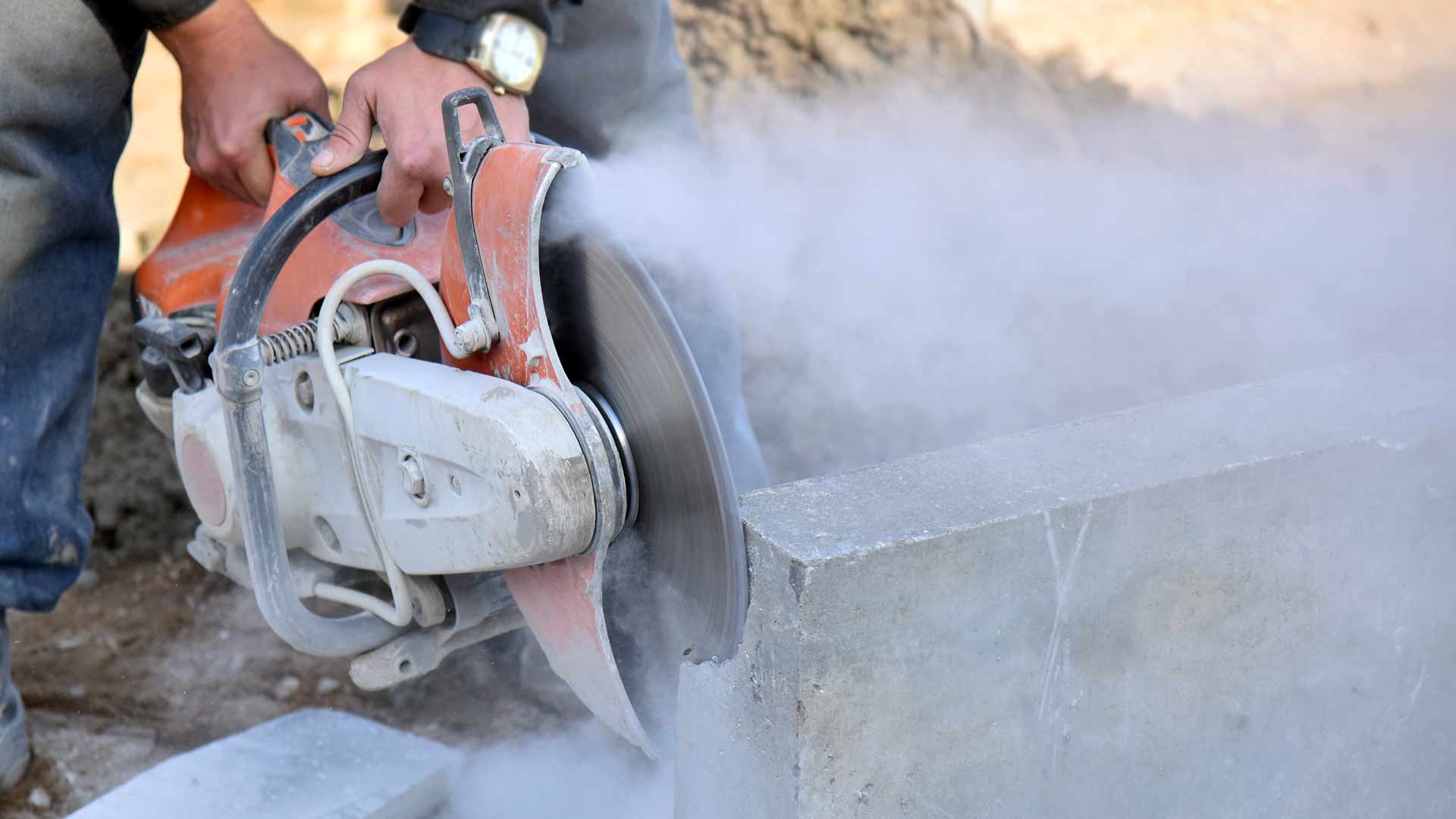
In many cases, eliminating silica dust is not practicable. Elimination means you completely remove the hazard from your workplace.
